Dr. Niazi's Bold Leap Forward
Imagine a world where the need for costly and unpredictable biological tests is replaced by a simple, yet powerful concept: thermodynamic equivalence. This innovative idea, spearheaded by Dr. Niazi, aims to transform how we assess drug equivalence, making it more efficient and accessible than ever before.
The FDA’s recognition of Dr. Niazi’s petition underscores their commitment to advancing regulatory science and embracing cutting-edge methodologies. This presents a unique opportunity for collaboration and innovation, where stakeholders can come together to shape the future of drug development.
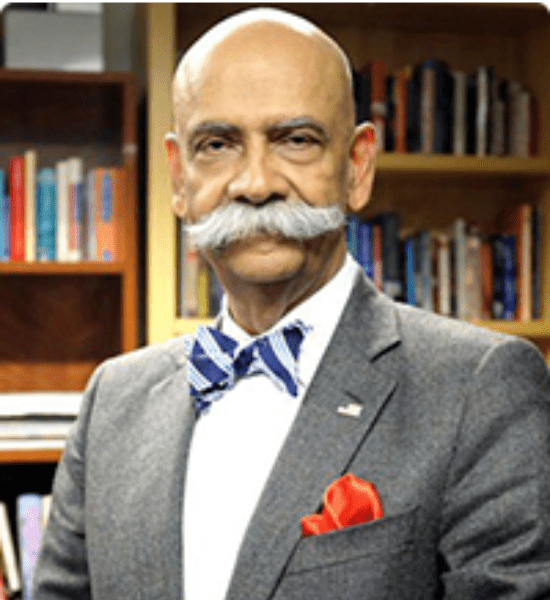
Fast to Market Biosomilar
I am now developing several biosimilars using this model and invite inquiry if you are interested in acquiring technology, or supply of finished product and any level of regulatory involvement–this model, now opens the opportunity for companies not associated with manufacturing to become the largest supplier of biosimilars. Following are the service ads associated with this exprtise:

Selecting the Right Product

Complete 351K Filing Map
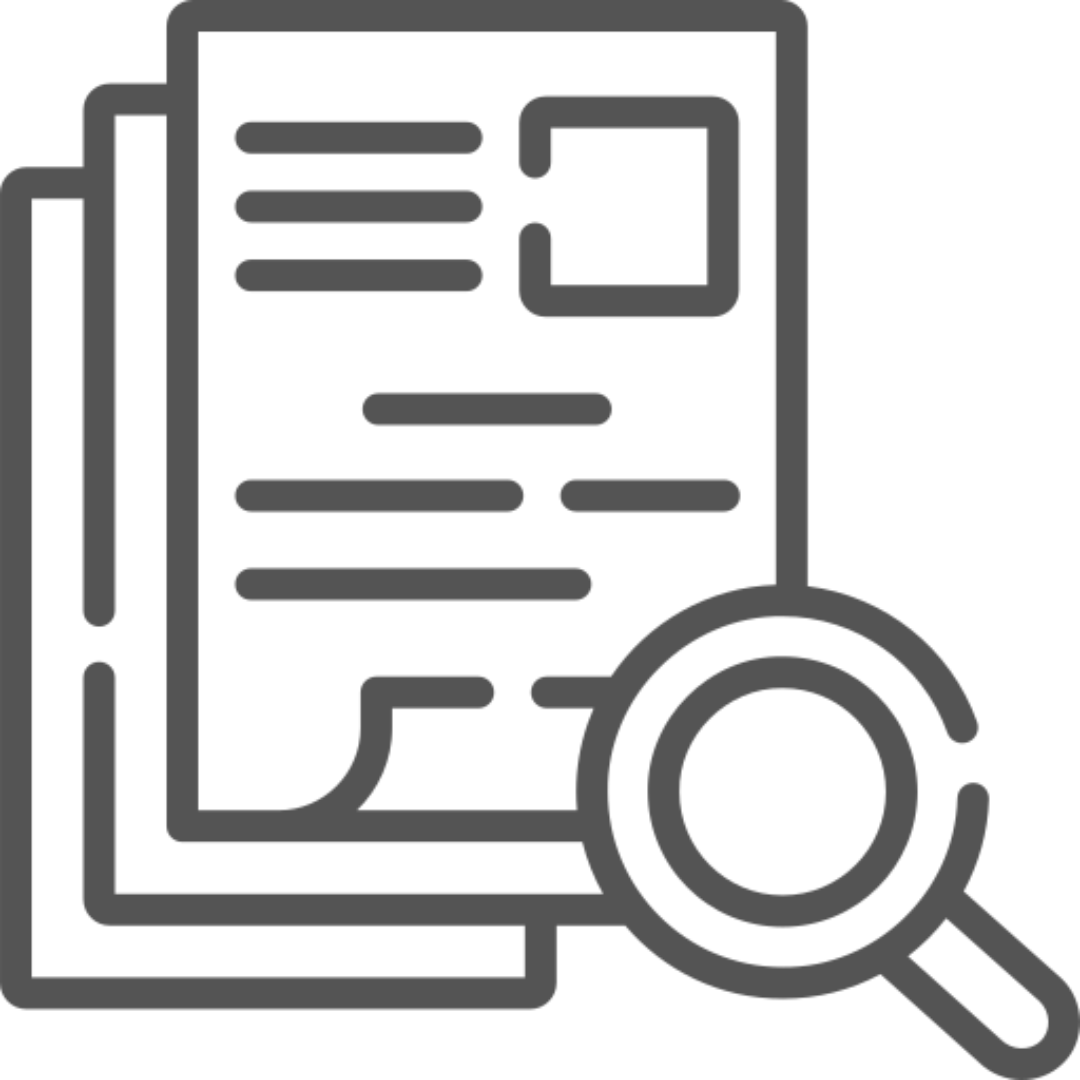
Review of BLA
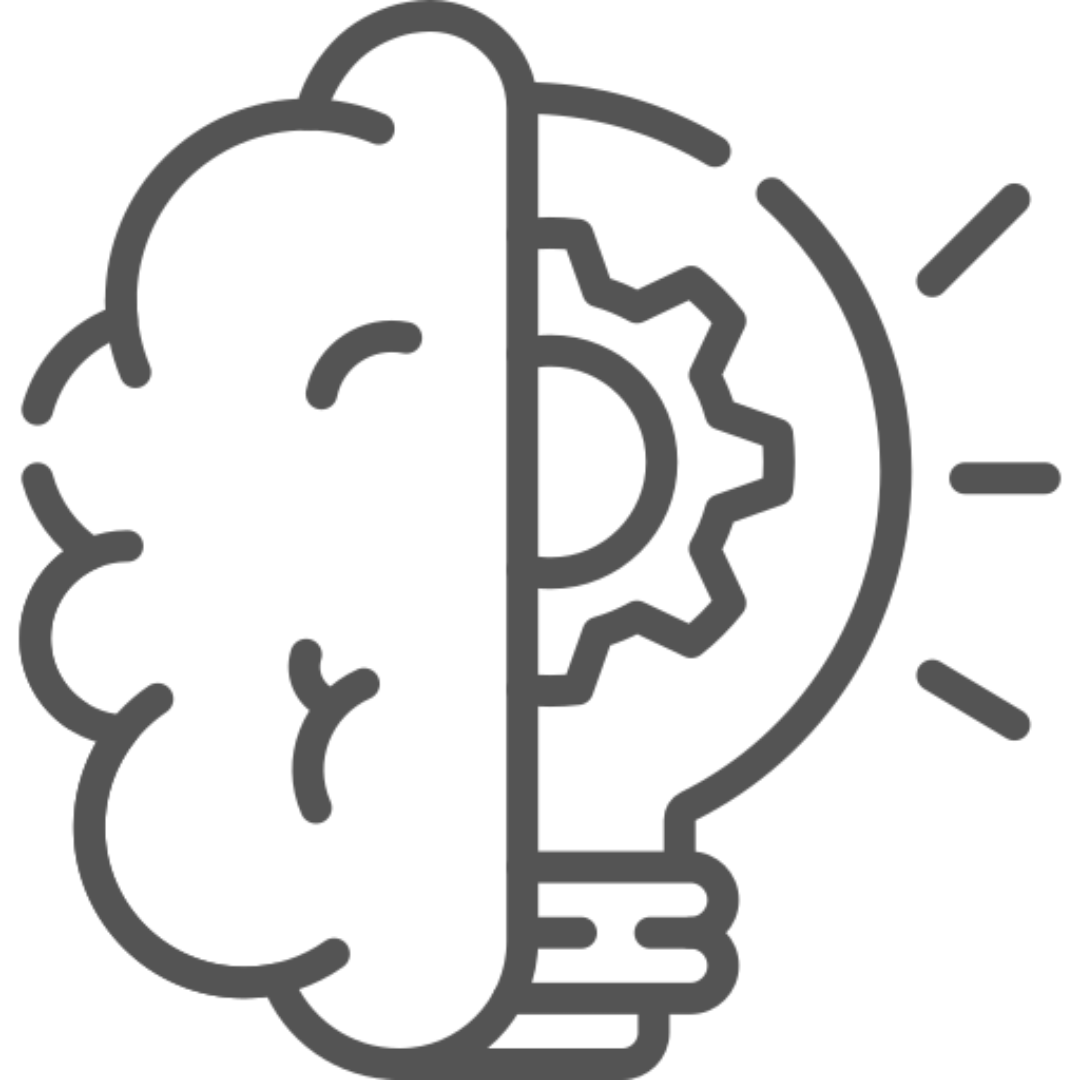
Bioprocessing Innovations
As biologics come off patent, one strategy used by the reference product owners is to create alternate delivery systems, higher concentration being one of the most important. Can you justify to FDA a 351k with a different formulation; yes, you can, if you can dig into scientific justification.
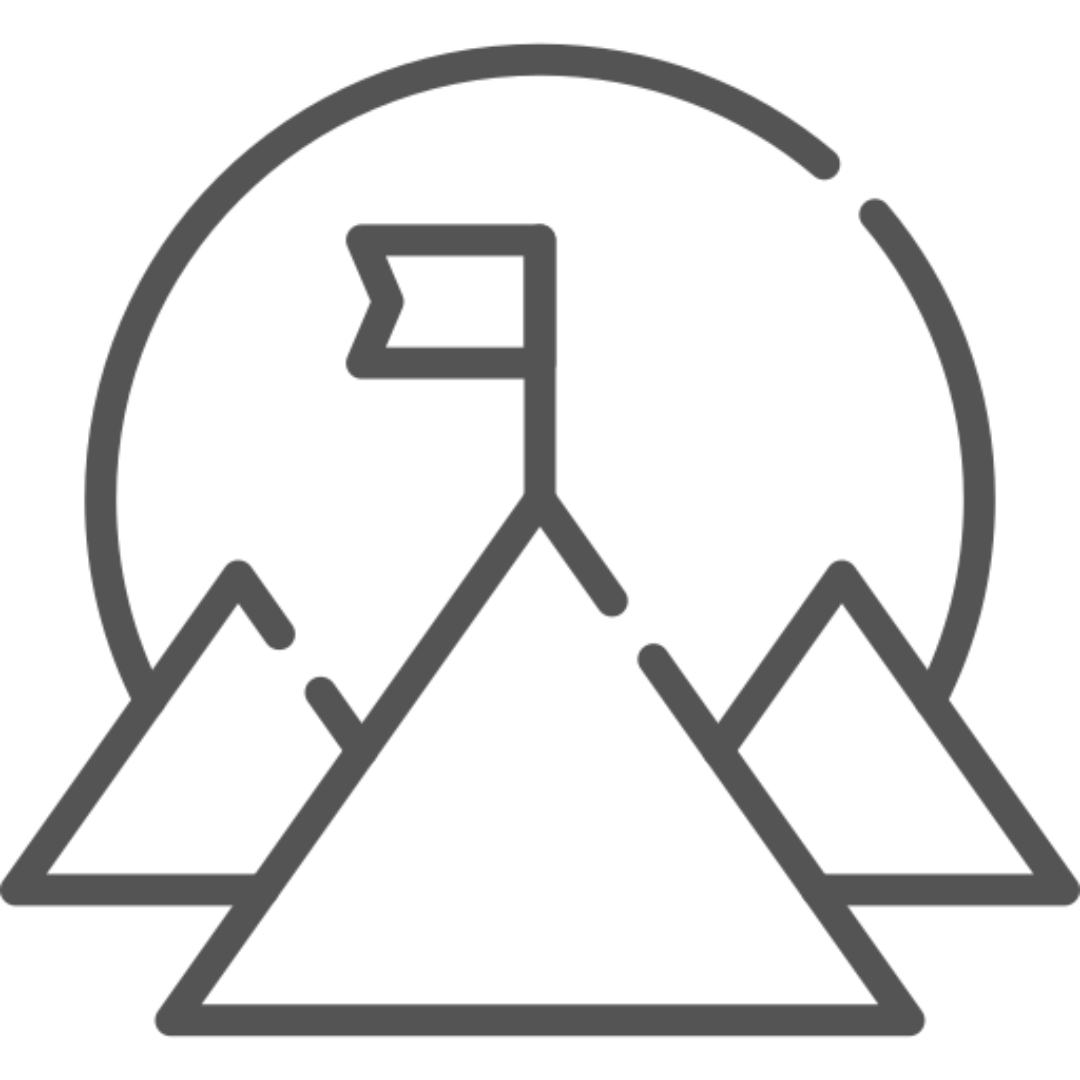
351k and 505(b)(2) Submissions
Managing Cogs of Biological Drugs
Low Cost Manufacturing
The risk-based GMP establishes measures to assure safety of the product; decades ago, the industry adopted a facility design that was hard-walled model but now we have better technology to justify alternate designs of much lower cost, in both capital and maintenance. I have patented several designs that allow manufacturing in ISO9 environment.
Single Use Manufacturing
The future of biological manufacturing is undoubtedly in single-use elements; having written a book on the subject, I can assist in creating a compliant facility where the challenges of leachable are minimized and COGS reduced substantially.
Minimizing Variability Due to PTMs
Nothing produces more variability than the stress on the cells and expressed proteins. Several proprietary and patented methods now allow achieving high consistency of structure, besides increasing the total yield, to allow faster development of biosimilars.
Single Container Manufacturing
The classical upstream/downstream model can be redefined by focussing on the expressed molecule; dozens of patents that I own allow expressing and purifying the biological molecule in a single container allowing faster development of clinical supplies.
Continuous Manufacturing
A long-sight dream is now possible using a train of single-use containers feeding down to recover expressed protein continuously reducing contamination risk and COGS, as well as constraints on the facility size.
Clinical Supplies from Smaller Facilities
New drugs, biosimilars and any alternations thereof need to be manufactured in facilities that cost hundreds of millions to offer a clinical supply; what if we have a system that does not require a GMP-certified facility to produce a safe product? We now do have this opportunity opening the door to R&D organizations and smaller companies to seek out the fast expanding market of biologics.
GMP Manufacturing Facility
Patented HVAC Design to Reduce Cost by 70-80%
Single-Use Systems to Reduce Utilities
Continuous Automated Compliance